Optimizing Material Usage:
Increased Accuracy Directly Impacts the Bottom Line.
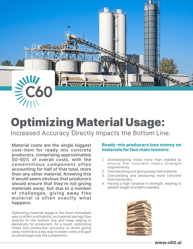
Download the PDF version of this article
Material costs are the single biggest cost-item for ready mix concrete producers, comprising approximately 50-60% of overall costs, with the cementitious component often accounting for half of that total, more than any other material. Knowing this it would seem obvious that producers should ensure that they’re not giving materials away, but due to a number of challenges, giving away free material is often exactly what happens.
Optimizing material usage is the most immediate way to affect profitability, as material savings flow directly to the bottom line and keep paying in perpetuity for producers. As a result, optimizing mixes and production accuracy to avoid giving away material is a key way to lower costs and gain an advantage over the competition.
Ready-mix producers lose money on materials for four main reasons:
- Overdesigning mixes more than needed to ensure the concrete meets strength requirements.
- Overbatching and giving away free material.
- Overyielding and producing more concrete than necessary.
- Having a high variance in strength, leading to greater target strengths needed.
Design Optimization
Producers are required to meet the specified strength performance when they sell concrete. Typically, producers put more cement into a mix than necessary to be sure they achieve the required strength.
If a mix under-performs the specified strength—even by a small amount—the producer risks liability, and reputational damage. All mixes have variability in strength performance, so producers often overdesign to ensure the strength will still pass. Especially in more-conservative markets like the United States, it can be easier and safer to unnecessarily add additional cement as “insurance” if a producer lacks the tools or resources to truly understand mix design and material use. Often, producers know there are savings opportunities in mixes, but are overwhelmed by time, design constraints and the risk of underperformance.
Often, they don’t have the tools, time, or expertise to quantify average strength, variability, and cementing efficiency in order to pinpoint the exact cement contents that will lead to compliant strength results with the minimum over-design needed.
Producers operating in the United States also face challenges resulting from a more prescriptive-based approach to mix design. Typically, if the mix is not prescribed outright, there are a series of materials constraints to comply with, and full mix constituents must be submitted for review and approval prior to project start. Once the project is underway, if the mix is overperforming the producer is still contractually obligated to make the mix as submitted, presenting barriers to optimization for that project. However, the producer inevitably will receive the same mix request on future projects, and by analyzing past performance can identify opportunities to optimize and submit a more-accurate ingredient list to future customers. It may also be possible to make adjustments to in-progress projects through re-submission of ingredients even if that means sharing savings with the contractor or owner in order to incentivize them to consider approving the optimized mix design. Constraints tend to be viewed as barriers, but with the right tools and knowledge, constraints can be viewed as opportunities for future optimization and cost savings.
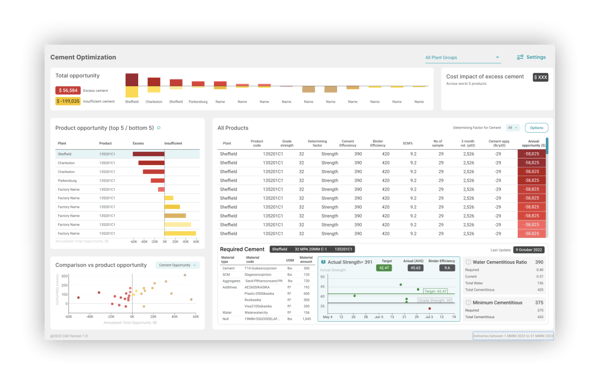
Batch Optimization
It’s common for plants to accept out-of-tolerance batches simply because they are minor, but a lot of minor errors can add up to a large saving opportunity. Often a bathcer or plant controller is focused on ensuring timely deliveries, and simply accept slight batching errors as it si only “a few dollars” While overbatching one or even 10 loads may have a minimal impact, the amount of money lost due to overbatching can be significant when it occurs repeatedly over time—and especially if many mixes spread out over multiple plants are involved.
The key is to find a balance between speed and accuracy for concrete production. Batching needs to be fast enough to meet demand and keep costs low, while being accurate enough to protect profitability.
By having information on a holistic scale across all materials and all plants, managers can identify whether overbatching is a singular instance, or a reoccurring pattern and opportunity to save money. Though managers often have the ability to run batching reports, they infrequently run reports as often or as holistically as necessary to make informed decisions. It can take many hours every week to analyse reports about every batch at every plant and then analyze the results.
An analogy is driving a car, , drivers know they should check their tire pressure before a trip. Realistically, they only check occasionally—and sometimes only when the monitoring system alerts them of a problem. C60 is like that monitoring system, alerting producers to problems instantly. It provides analyzed information across the entire portfolio in seconds.
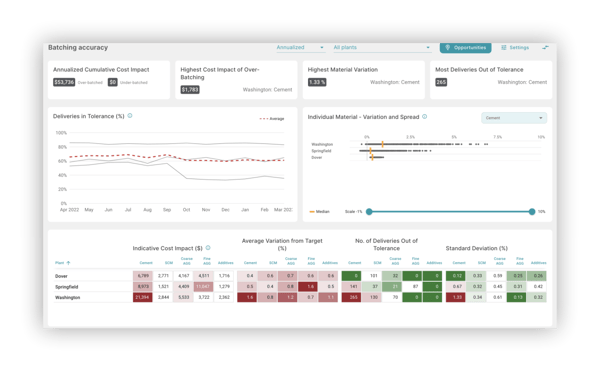
Yield Optimization
Some producers have thousands of mix designs. They may have mix management systems, but no single place to view all mixes at all plants at the same time. With frequent raw material and mix design changes, a small change could push a mix out of yield, wasting money. It may be pennies per yard, but costs add up for producers making many yards.
Typically, producers should test characteristics like specific gravity, but often this is done too infrequently for incoming raw materials. Testing density of raw materials weekly, daily or even more frequently can ensure accurate yielding. Without a way to test and analyze results, general managers tend to simply use averages and this leads to conservativeness and overyielding.
Another analogy, if you’re driving a car without a speedometer and know there are cameras monitoring speed, you drive slower to ensure compliance. You may not get pulled over, but you will arrive at your destination slower. Alternatively, if you have an accurate speedometer, you will drive exactly the speed limit, wasting no time and proceeding without risk. C60s yield dashboard identifies all out-of-yield mixes, the amount they are out of yield, and which plant produces the mixes to ensure accuracy.
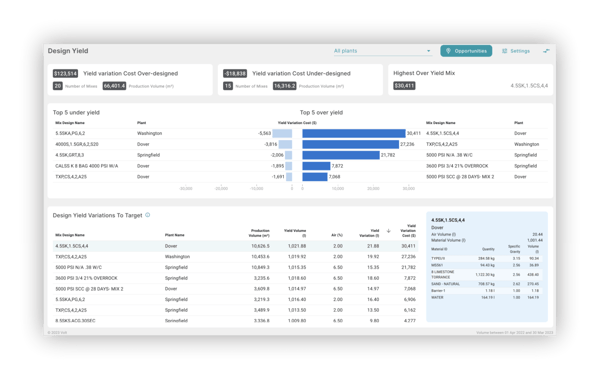
Data Leads to
High-Impact Decision-Making
Optimizing materials takes a different skill set than most managers have, as they tend to rise to the position through the operations side of production. Optimizing materials takes a holistic understanding of engineering and quality control.
Additionally, producers—especially those that are small- and medium-sized businesses sometimes lack a sufficient resources dedicated to a quality control program. They may have one person who tests quality, but no manager or expert at the leadership level experienced in quality control who has the skills needed to analyze mixes and determine optimization solutions. Often, quality control is thought of as extra overhead instead of an opportunity to improve profit margins.
That mindset typically changes as producers grow and add multiple plants and mixes as they realize the opportunity that exists in materials which represents over 50% of their costs. With growth, it becomes imperative to pay attention to details like material usage and mix optimization because increased size creates increased risk and opportunity. A good quality control program should include testing frequency, data collection, data analysis and data-driven risk analysis. These characteristics allow producers to set appropriate risk parameters and manage mix performance to those criteria.
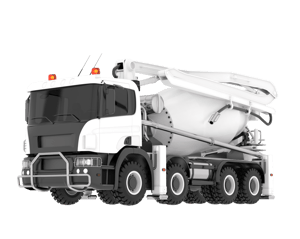
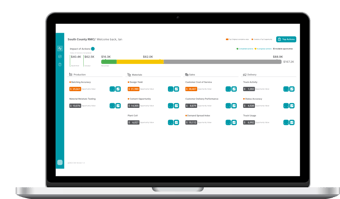
Technology like C60 provides a consolidative management view of batching and mix optimization across all plants, enabling a quick and accurate glance at operations to compare plants and identify areas for material optimization. C60 allows managers of ready-mix producers to view a report with accurate management information – not just data to identify areas for improvement in optimizing material usage and the bottom line.
The next article in this five-part series on solving common business challenges to improve profitability will cover ways to get the most out of your fleet. Take a look at our first article that covers the top four profitability drivers impacting ready-mix business leaders for a bird’s-eye look at improving the bottom line and the second article on getting to the right price.
Get full access to our articles delivered right to your inbox.
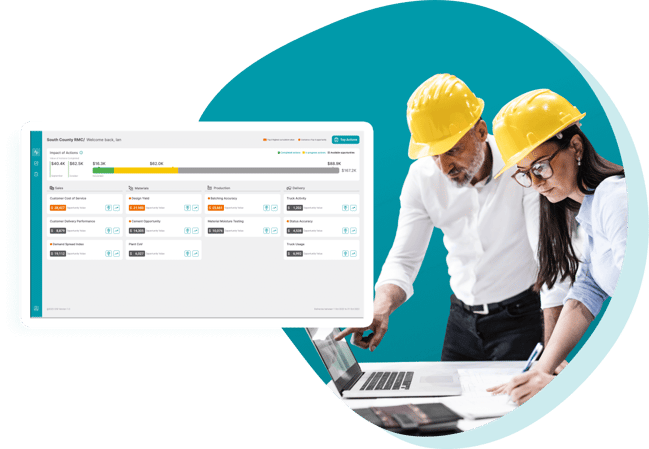
C60 is the culmination of decades of experience from C60’s co-inventors who spent years working to optimize the way ready-mix producers find efficiencies in their business. Their experience and know-how have been applied in over 30 countries and more than 1,500 concrete plants.
At C60, we’ve assembled a team from the RMC industry, using software and analytics to bring you the first opportunity platform that puts dollars back into the pockets of RMC producers. For more information or a demo, view our website, www.c60.ai, or contact us at sales@c60.ai or 1 (760) 219-8718 or 1 (514) 909-9231.
To see how C60 helps busy GM’s and RMC executives like yourself, contact one of our ready-mix experts for a personalized demo. C60 is in the business of helping producers drive more profitability.